聚苯硫醚(PPS)是一种新型高性能热塑性树脂,具有优良的耐热性、阻燃性、绝缘性和耐腐蚀性,属于特种工程塑料。
经过复合改性后,PPS转变为特殊的工程塑料,具有不同的性能和用途类别。它是迄今为止全球最具成本效益的特种工程塑料,被誉为世界上使用最广泛的特种工程塑料。PPS由于产能的增加和成本的降低,被列入通用工程塑料排名,成为继聚碳酸酯、聚酯、聚甲醛、尼龙、聚苯醚之后的第六大工程塑料。
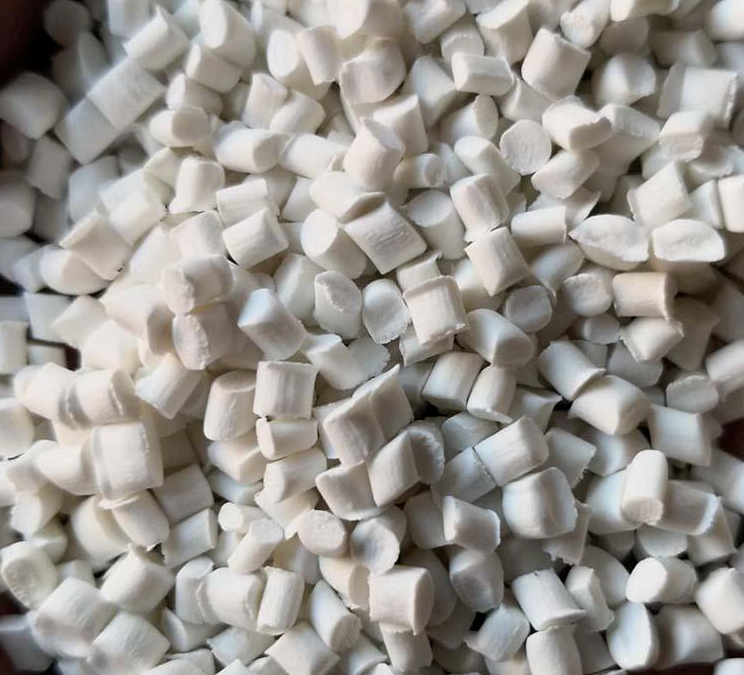
PPS具有优良的耐高温、耐腐蚀、耐辐射、阻燃和均衡的物理机械性能,同时还具有优良的尺寸稳定性和优良的电气性能。在汽车、电子电气、纺织、环保、建材等行业得到广泛应用。其应用领域如图1所示。
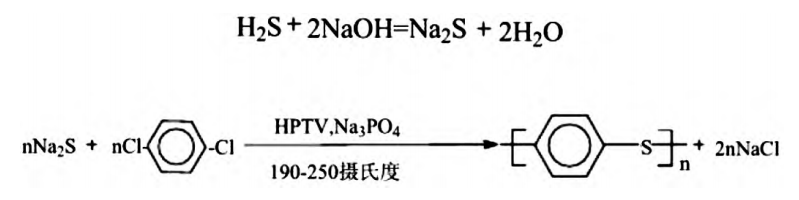
目前PPS有多种合成方法,可用于工业生产的主要有硫化钠法和硫磺溶液法。日本武裕曾采用硫溶液法,后因硫磺溶液法缺陷不易解决而作废。因此,目前国内外生产厂家多采用间歇式硫化钠法合成PPS树脂。
除这2种方法外,合成PPS的方法还有氧化聚合法、对卤代苯硫酚盐自缩聚法、硫化氢法等。其中,国内厂家已有硫化氢法的尝试,但由于存在反应速度过快等缺陷,目前基本未采用该方法。
此方法是最早生产PPS的方法,也是现阶段工业化或具有工业化价值的路线之一。主要通过二氯苯与无水硫化钠在极性溶剂中缩合反应制得PPS聚合物。
常用的极性溶剂主要有N-甲基吡咯烷酮(NMP)、吡啶、N,N-二甲基甲酰胺(DMF)、N,N-二甲基乙酰胺、N-甲基脯氨酸、六甲基磷酰三胺(HMPA)等。其中NMP、HMPA和N-甲基脯氨酸通常用于工业化生产。硫化钠法合成反应式见图2。
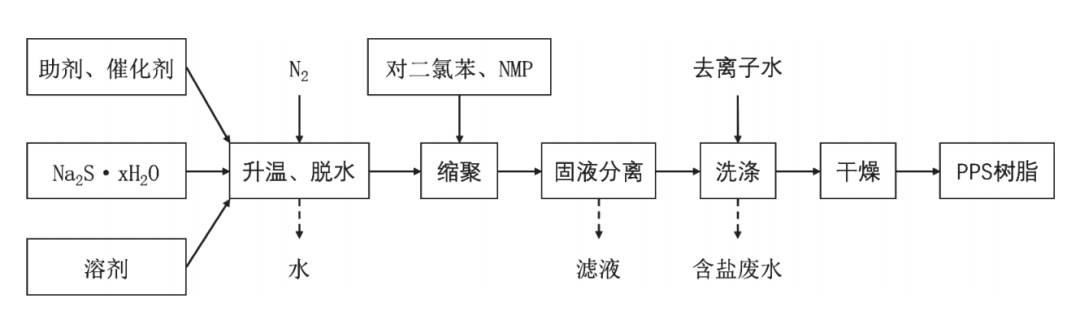
这种方法原料易得、产品质量好。但早期的工业化过程中存在生产工艺较长,原料难提炼等缺点。PPS中含有少量的钠离子,使产品的防潮性、耐电性、成型性降低。主要产品为线性、半交联、交联三大类。
该方法的工艺难点之一是用于反应的硫化钠不需要含有结晶水,而对于正常结晶水来说,硫化钠脱水的难度较大,且目前生产厂家通常在反应器中采用非均质的方法脱水,再进行聚合。
硫磺溶液法又称硫磺法。此法用硫磺代替硫化钠在约220℃的条件下,以六甲基磷酰三胺或N-甲基吡咯烷酮为溶剂,对二氯苯和硫磺在常压下缩聚制备PPS,反应收率大于80%。硫磺溶液法合成反应式见图3。
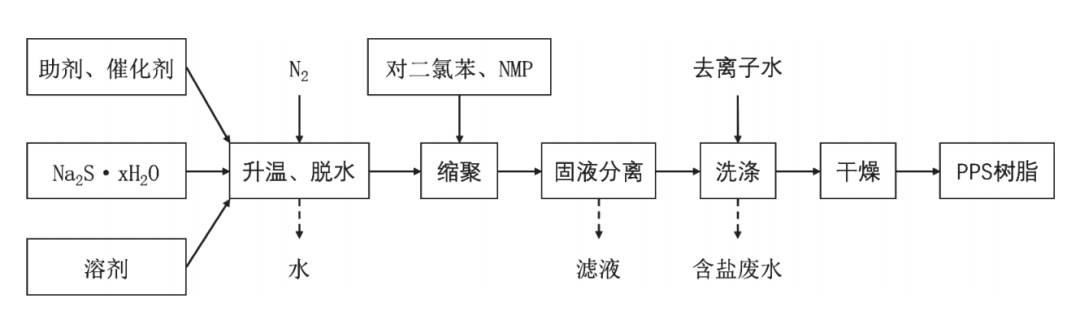
硫磺溶液法的优点是原料硫磺丰富,价格便宜,易得,产品质量好,工艺短,副产物少;不足之处是技术难度大,副产物不易去除。
氧化聚合制备工艺是以二苯基二硫为原料,以氧气或空气为氧化剂,以乙酸丙酮氧化钒为催化剂,经氧化聚合而制得的一种线性聚苯基硫醚树脂。
该方法的收率很高,几乎为100%。此外,产品纯度也高,无支化、环状、交联等现象,没有副产物氯化钠,可防止金属离子对PPS耐久性的影响。
但反应后期会产生过硫化物,使链式增长反应停止。另外,该法制备的PPS树脂相对分子质量不高、黏度低、加工性能差,不具备实用价值。
此种方法以对卤代苯硫酚为原料,线性PPS树脂是在熔融状态下由对卤代硫酚自缩聚而成。卤代苯硫酚盐熔融反应式见图4。

该方法无需调整单体比例,副产物少,但单体生产工艺复杂,成本高,个别单体有毒,副反应易产生环状PPS,从而起到阻止相对分子质量增长的作用。
硫化氢法是以硫化氢、氢氧化钠、对二氯苯为原料,以碱金属盐为助剂,在极性溶剂中通过混合的方式,制备出线性高相对分子质量PPS树脂。硫化氢反应式见图5。
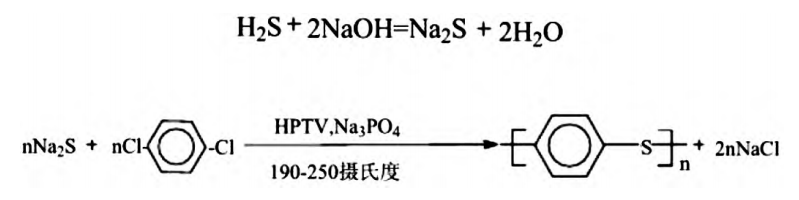
这种方法的优点是副反应较少,产物具有较高的线性度。缺点是反应速度过快,硫化氢腐蚀性强,对生产装置和长期反应工艺要求较高。
综上多种方法对比,鉴于目前原料硫磺丰富,价格便宜,易得,为此厂家大多采用硫化钠法合成PPS树脂,产品质量好,工艺流程短,副产物少。
文中主要对硫化钠法合成PPS的工艺进行了详细阐述。硫化钠法主要以对二氯苯(PDCB)和硫化钠为原材料,以极性有机溶剂N-甲基吡咯烷酮(NMP)和碱金属盐为催化剂和助剂,在高温高压条件下反应生成PPS和氯化钠。采用硫化钠法合成PPS的过程如图6所示。
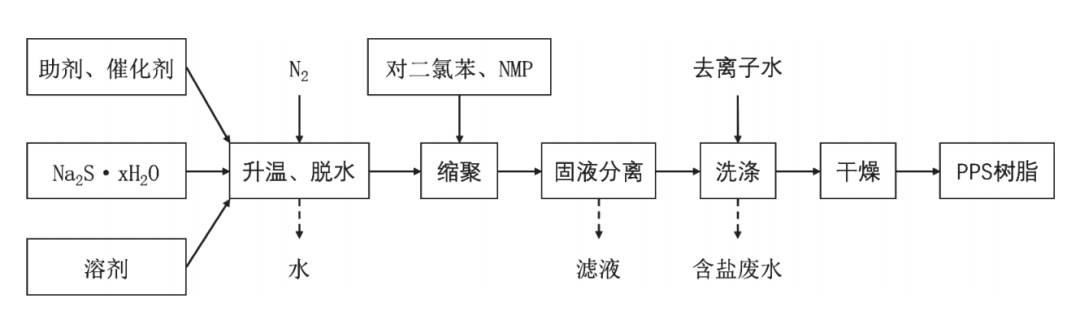
硫化钠法PPS合成工艺:
①按一定摩尔比向反应器中加入含水Na2S、极性溶剂NMP、催化剂、助剂等,用N2置换,然后在反应器中进行加热分离脱水,并通过脱水塔分离NMP和水,使NMP返回反应器中。
观察分离脱水速率,如果反应器脱水率满足要求,即可将反应器温度适当降低运行,同时脱除的废水送至废水系统进行处理。
②将一定量的PDCB和NMP加入反应器中,同时将反应器的温度升至规定温度后保温,进行第一次反应,再持续升温至要求的反应温度后保温,进行第二次反应。
待反应过程全部结束后,再将反应器温度降至要求温度后放料,利用固液分离器分离,有机滤液送至NMP回收系统,回收NMP再利用;滤饼转移至打浆釜中,加入定量的水打浆洗涤,再通过固液分离器分离,滤液送至废水系统处理,回收废盐;滤饼经多次洗涤,直至滤液中NaCl含量达到要求范围为止。
③洗涤装置中剩余固体物料输送送至干燥装置中,干燥后即可得到PPS成品。

硫化钠法合成PPS反应所选取的原料主要是含结晶水的硫化钠和对二氯苯。如果原料配比不当,在合成时易造成反应失衡,对反应后的产物有较大影响,如副产物增多、相对分子质量降低、生产成本上升等。
经过多次试验表明:在PPS的实际生产过程中,含水硫化钠与PDCB的原料摩尔配比控制在1∶1.05范围内效果较佳。
反应物配料选取的硫化钠脱水方式主要有:反应器外脱水、共沸式脱水和反应器内直接脱水等3种。
其中反应器外脱水是在真空干燥装置内进行的,选取真空度≥0.095MPa、温度范围在45~120℃,脱水约4h等条件。但是此种方式存在的缺点就是整个脱水过程耗时较长,安全风险性大,操作繁琐,还容易出现粘壁、结块等问题,为此在合成过程中很少采用此方式;
反应器中的共沸脱水需要添加额外的低沸点惰性溶剂,在低沸点惰性溶剂达到共沸时去除反应器中的水,此种方式的缺点就是成本更高,脱水过程较长。
反应器内直接脱水是在氮气保护下直接加热脱水。该方式实际生产过程中较为简单,成本低,为此通常采用此方式。
基于硫化钠法合成PPS工艺可以看出,应选择强极性溶剂,如NMP和HMPA,实际生产中,NMP被广泛使用。目前,NMP溶剂回收主要采用水洗滤饼回收NMP和萃取回收NMP的工艺。水洗滤饼NMP循环利用工艺具有操作更方便、成本更低等优点,因而被广泛采用。
催化剂和助剂有利于提高大分子聚合物在溶液中的溶解度,从而有效增加PPS的收率。但是,如果催化剂和助剂投入量过大,就会使聚合物析出。
目前,在工业生产中使用的催化剂有LiCl、MgCl2、AlCl3、苯甲酸锂、硬脂酸锂、乙酸锂、乙酸钠、己内酰胺等。而常用的助剂都是一些无机酸或有机酸的碱金属盐如Na2CO3、NaOH、苯甲酸盐、磷酸盐等。由于目前常用的催化剂和助剂有毒性且成本较高,可利用合成工艺中再回收方法回收,用于下一批PPS的合成反应。
聚合反应温度和时间是PPS合成的重要工艺条件。聚合反应温度不宜过高,通常采用二段保温方式进行聚合。由于聚合反应是放热过程,需要导热油系统和DCS控制系统精细控制,使反应温度控制在要求范围内。
若聚合反应温度过高,会导致反应过程失衡,副反应增多;若聚合反应温度过低,PDCB与苯环的反应活性随之降低,不利于反应的平稳进行。一般来说,第一次聚合温度控制在220~260℃左右,反应时间控制在1~6h,第二次聚合温度控制在260~290℃左右,反应时间控制在1~4h。
聚合反应产物固液分离后的滤饼主要成分为PPS树脂、NMP、NaCl、极少量的PDCB、副反应物等。
为了获得纯PPS树脂,通常使用水洗工艺。由于聚合反应过程中高分子聚合物结晶过程会包裹部分无机盐,洗涤过程中,聚合物颗粒包裹的无机盐等成分无法释放,造成PPS树脂洗涤效果差,灰分含量高。
因此,通常使用高温高压水洗方式进行清洗,在高温下PPS树脂沿着分子链缓慢疏松,残留的无机盐等成分释放到水相中,实现降低PPS树脂灰分的效果。
通过综合比较常见的PPS合成方法的优缺点,发现硫化钠法合成的PPS产品具有质量好、工艺流程短、副产物少等优势。
参考资料:线性高相对分子质量聚苯硫醚树脂的合成研究,浙江新和成股份有限公司,李沃源
原文始发于微信公众号(艾邦高分子):线性高分子量PPS的合成工艺研究