2024年全球尼龙产能突破1000万吨,中国市场消费量年复合增长率达7.5%,其应用场景正从传统工业向新能源、生物医疗等前沿领域延伸。然而,随着材料科学的进步与产业需求的升级,尼龙早已突破传统纺织和机械领域的局限,化身为跨行业应用的“多面手”。从汽车轻量化的核心部件到生物医疗的精密植入材料,从工业机器人的精密齿轮到深海探测的耐压浮力装置,尼龙正以惊人的创新速度重塑现代工业的边界。
尼龙产业家族庞大,产品种类繁多,品种主要有尼龙6、尼龙66、尼龙610、尼龙11、尼龙12五大品种。
此外,还有尼龙56、尼龙4、尼龙8、尼龙9、尼龙810及各种共聚改性尼龙。尼龙6和尼龙66两者消费量约占尼龙总消费量的90%。尼龙6和尼龙66在民用及工业用下游普遍应用,尼龙6主要用做尼龙纤维和工程塑料,尼龙66主要用做工程树脂及工业用丝。
一、汽车轻量化:尼龙重塑交通工具的未来
在汽车行业的发展进程中,新材料的应用一直是推动其不断进步的关键因素之一。我国汽车行业产能增长如骏马奔腾般迅猛,车用工程塑料产业也随之迎来了广阔的发展空间。如今,工程塑料正以一种势不可挡的姿态取代金属材料,从最初的装饰件逐渐迈向结构件与功能件的重要领域。而在众多工程塑料中,PA(聚酰胺)材料凭借其卓越的性能,在汽车行业中崭露头角,尤其是PA6、PA66、PA12等尼龙材料,正发挥着越来越重要的作用。2025 年全国新能源汽车销量将达到700万~900万辆,2030年将达到1700万~1900万辆,2030年车用PA材料用量将达到144万吨。
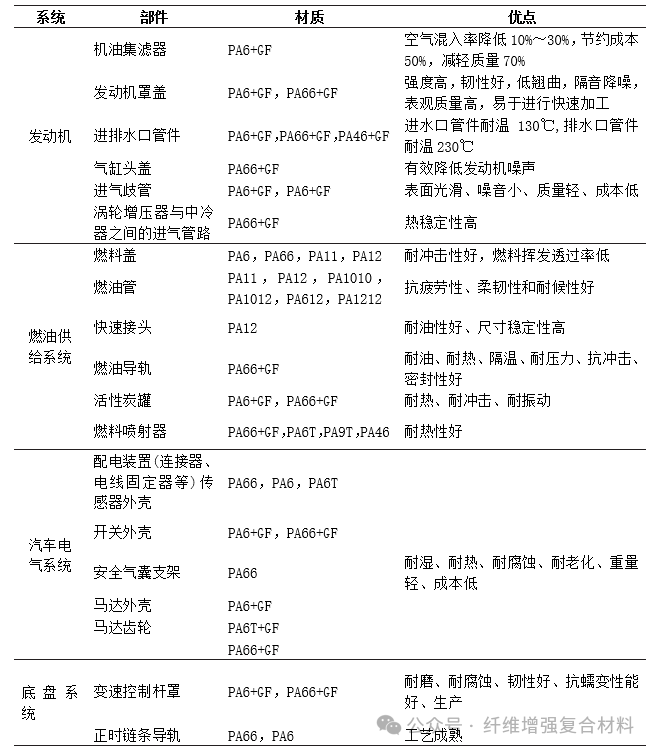
尼龙在汽车轻量化中的核心应用始于发动机周边部件。传统金属材料如铸铁和铝合金因重量大、加工复杂而逐渐被高性能尼龙取代。例如:
进气歧管:进气歧管是发动机的核心部件,它是影响发动机动力性和油耗的关键因素之一。其功能是为发动机各缸提供充足而均匀的混合气,同时为主要的传感器和执行器提供结构支撑。一般的进气歧管采用铸铁和铝合金材料,20世纪80年代以来,相继开发成功了用尼龙通过熔芯法和磨擦焊接法来制造进气歧管。用尼龙制造空气进气歧管代表了塑料代替金属的真正突破。由于设计的灵活性,使产品装配更方便,再配以功能集成,可使主机厂和一级供应商在生产效益和成本方面获益。与铝合金比较,塑料进气歧管可以减轻40%左右的重量,生产成本降低20%~30%,同时通过部件集成还可以进一步减低成本。另外,由于进气歧管的内壁光滑,从而有利于提高发动机的动力性和燃油的经济性。进气歧管目前主要的生产方法是采用振动摩擦焊接技术,也有采用熔芯法等生产一些复杂的、小批量的产品。通常尼龙进气歧管采用的材料30%-35%玻璃纤维增强尼龙(PA6/PA66)制成的进气歧管。
油底壳:油底壳作为汽车零部件的一个重要部分,从铸铝件一步一步发展到用增强尼龙材料注塑件,如PA66+GF35、PA6+GF35等已成为汽车发动机油底壳轻量化的新型材料之一。PA66+GF35注塑件比铝合金压铸件减重30%-40%。尼龙材料的成型加工性良好,使得部件壁厚变化、局部加强筋设计、倒扣结构、多重法兰、与其他部件集成为一体化的可能性大大增强。如:采用高流动性和高强度聚酰胺设计制造油底壳,在其结构上,已集成了油道、吸油管、机油过滤器、单独的备用油口和防溅板等,不但保持了整个部件外廓尺寸不变(与铝合金材料压铸件相同),而且整个油底壳部件的储油容积扩大了30%。由于机油容量的增加,汽车发动机的机油更换周期和保养间隔可延长50%。大量统计资料表明,尼龙材料油底壳的生产成本要比压铸铝合金材料油底壳低 30%~40%
2. 轻量化的核心引擎
新能源汽车的爆发式增长推动轻量化需求激增。研究显示,汽车每减重100kg,燃油车油耗降低0.3-0.6L/百公里,电动车续航提升6%-11%。尼龙材料的应用不仅降低了生产成本(模具寿命为铝合金的10倍),更推动了新能源汽车市场渗透率的快速提升。
尼龙凭借密度低(1.14g/cm³)、比强度高(拉伸强度达80-120MPa)、耐油性好等优势,成为 “以塑代钢” 的首选材料。例如,雪佛兰Equinox EV采用巴斯夫玻璃纤维增强尼龙6制造外门把手套管,集成金属部件后减重30%,生产效率提升40%。丰田2024款车型首次使用尼龙树脂框架打造动力学座椅,重量减少30%,成本降低20%。
动力系统:尼龙66与玻璃纤维复合材料(如杜邦 Zytel®)替代铝合金制造电池包壳体,重量减轻40%,同时满足IP67防水等级。特斯拉Model Y的电池模组支架采用长玻纤增强尼龙,抗冲击性能提升50%,热膨胀系数与电芯匹配度达98%。
3. 技术挑战与解决方案
二、生物医疗:从辅助器械到精准医疗的跨越
医用卫生高分子材料,特别是植入类的医用高分子材料,应满足无毒性、化学惰性、组织相容性、血液相容性、耐生物老化性、可消毒性、不致癌以及易加工等性能,以保证材料对人体的安全性。
PA材料与天然人体组分蛋白质大分子具有相似的酰胺类结构,具有良好的生物相容性,不易使生物体细胞产生刺激信号。
此外,其还具有良好的化学稳定性和可控的机械性能等。同时,细胞可以吸附在PA材料表面。这些特殊性质都使PA医卫材料,特别是植入PA材料在减轻质量、改变力学性能、特别是在促进植入PA材料与人体之间建立相互力学作用等方面起到有利作用。
PA被广泛用作医用缝合线、医用导管、导管球囊、牙种植体、抗菌复合材料、3D打印生物医用设备、骨生长支架、药物运输材料、伤口愈合敷料等医卫材料中。
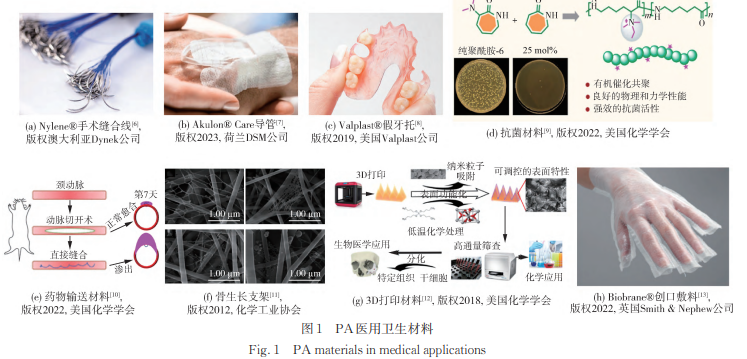
PA作为医用卫生材料时主要利用了其优秀的尺寸特性、力学性能、柔韧性、低吸湿性等。一般来说,PA通常作为短期植入材料如缝合线和假牙时,其植入时间小于21d,因此通常不考虑其细胞黏附性等特性。
1、PA缝合线
医用缝合线主要被用作缝合伤口、减少感染并且保护伤口下组织。金线、银线、铁线、钢线、动物肠线、动物毛发、蚕丝、树皮和植物纤维等材料都曾被用作或正被用作医用缝合线。
一些合成类材料,如聚乳酸⁃乙醇酸等也可被用作医用缝合线。然而,目前没有一种医用缝合线可以满足所有种类伤口缝合的医用需要。
医用缝合线的选择取决于伤口缝合区域的组织层数、伤口缝合区域张力、缝线放置深度、有无水肿、缝合线预计取出时间、缝合线强度、韧性、是否易打结、打结牢度以及是否可能引起炎症等。
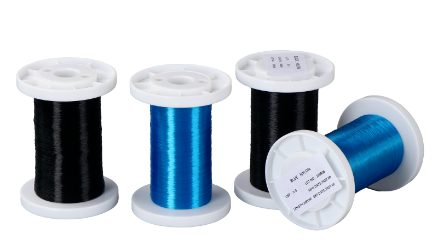
因此,目前医用缝合线的发展趋势是尽可能同时满足上述需求,另外加入其他功能,如药物输送、细胞运输、抗菌等以促进伤口愈合。制备医用缝合线的材料在性能方面需考虑长纤结构、纤维粗细、降解性能、抗张强度、表面结构、质感、刚度以及柔韧性等。
目前已经商业化的PA缝合线多由PA6或PA66制备得到,具有高强度、高细度以及高韧度。PA缝合线的特点是不可吸收、表面顺滑且具有低摩擦阻力、坚韧、有弹性。但与聚丙烯(PP)等缝合线相比,其缺点为打结性差,需要在缝合处打多个结节以确保伤口闭合。
目前临床使用的PA6或PA66医用缝合线主要为标准缝合线,包括长单丝结构、假长单丝结构、编织结构、双向带刺缝合线长单丝结构以及皮芯结构的PA缝合线。编织类PA缝合线由于其感染风险更高,因此使用率不高。目前广泛使用的PA缝合线为长单丝类材料。
在体内研究中,单丝或复丝PA缝合线的降解速度为15%~20%/年。一些常见的临床使用的非吸收PA缝合线的性质及应用如表1所示。不同牌号的缝合线具有不同的尺寸和直径。根据文献,并没有证据证明缝合针头或缝合线的尺寸对伤口并发症有影响。
然而,为了最大限度地减少组织损伤和组织内异物,缝合线应在满足抗拉强度的同时选择最小尺寸。单丝缝合线缝合伤口时阻力更低,而复丝缝合线具有较高的抗拉强度和柔韧性,但是与组织摩擦较大,同时存在造成术后缝合窦道和感染的风险。
因此,需根据患者和伤口实际需要进行手术缝合线的选择。
2、医用PA导管及球囊
医用导管是插入人体内的柔软中空管,有助于尿液引流或者在心脏病和肠胃病的诊断和治疗中用作各种应用的导丝器。PA医用导管也可以用在静脉滴注中,其主要可由PA6、PA66、PA11和PA12制备。
PA66制备的导尿管侧管在各项测试中表现出的性能与传统侧管一致,并可以将导尿管侧管的制备成本降低83.3%。在作为心脏导管的PA材料中,能够形成具有良好尺寸公差细管的能力是关键,其可以满足导管在极细血管中由于心脏跳动承受循环收缩压力的应用需要。
而在一些导管的顶端会配有柔软的球囊,其与导管可配套使用,起到扩张和清除血管中的堵塞、药物输送以及医用支架的运输等作用。
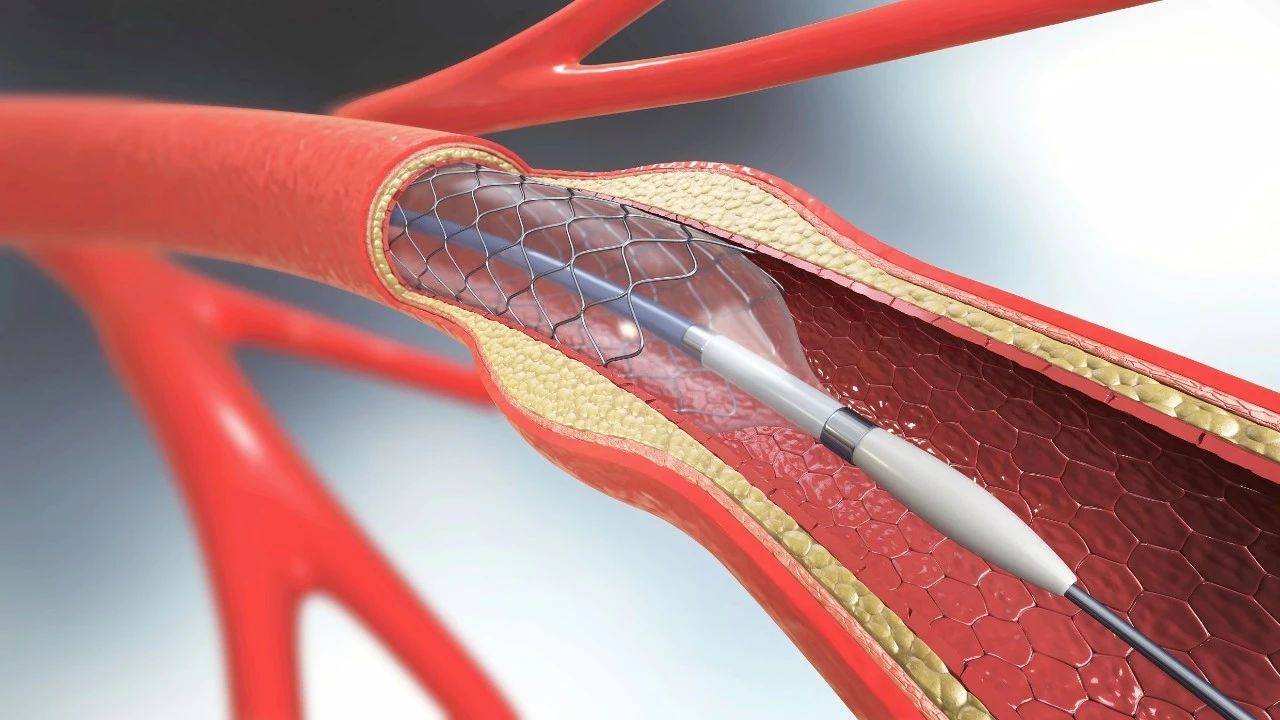
医用PA球囊材料通常由PA11和PA12制得,因为球囊材料在使用时需要在承受高压的同时保持其刚性结构,同时由于心脏导管内径的尺寸限制,PA材料需具有足够的韧性以满足尽量小的设计需要。
3、PA牙托材料
PA是一种理想的假牙基托材料,其韧性可以提供舒适性,同时其可以起到固定假牙的作用。同时,PA材料还具有高弹性,与非晶的PMMA相比,PA为结晶材料,具有低溶解性、高耐热性、高力学强度和高韧性。
此外,其还具有毒理安全性、低分解性。由于PA6比PA12亲水性更大,吸水性更强,因此PA6的尺寸稳定性比PA12差。
目前广泛被用作假牙基托材料的PA多为PA12,常见的销售商品牌号有Valplast®(PA12)、Bre⁃flex®(PA12)和Flexite®(PA弹性树脂)。在正常使用情况下,这些假牙托的使用寿命可以长达5年。
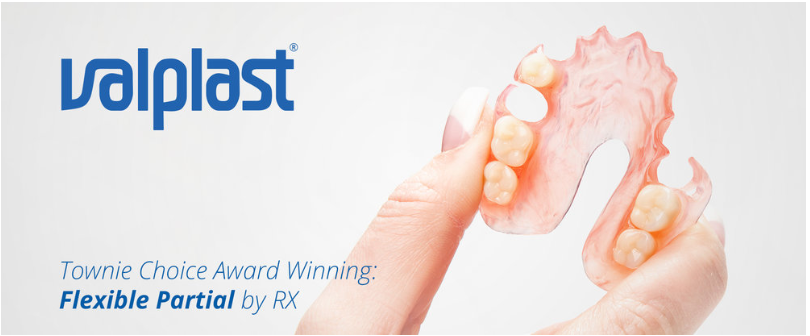
4、抗菌PA材料
PA医用卫生材料与人体组织接触或在体液环境中由于细菌等微生物滋生,可导致PA材料或仪器表面形成细菌生物膜,影响其医用性能,甚至导致强烈的免疫反应。
此外,细菌滋生极易造成感染,严重者可引起生命危险。因此,需要赋予PA医用卫生材料抗菌功能,以提高其使用安全性。可以通过向PA材料中加入无机/有机抗菌剂、抗生素等细菌灭活试剂,或者通过灭菌消杀方法获得清洁卫生的PA材料。
目前广泛使用的PA类抗菌材料大多是通过化学修饰方法得到的。
PA66纤维或织料可以通过将其表面化学改性,接枝氯胺类化合物从而获得杀菌功能。氯胺类化合物的N—Cl键在水中可以断裂生成具有强氧化性的活性氯成分,其可以非选择性氧化灭活各种细菌微生物,从而实现PA材料的自清洁和抗菌功能。
此外,抗菌后的PA⁃氯胺材料经过氯活化后又可重新获得抗菌性能,可以实现抗菌材料的循环使用。
5、3D打印PA医卫材料
3D打印可以将PA材料转为特定大小、形状的医卫材料零部件,从而满足不同应用场景的需求。3D打印PA材料可以被应用于牙科和整形领域。例如,利用3D打印制备PA6⁃Al⁃Al2O3复合长纤材料可以被应用于医用材料领域。
此外,还可以利用3D打印技术制备得到PA645膝盖植入材料。
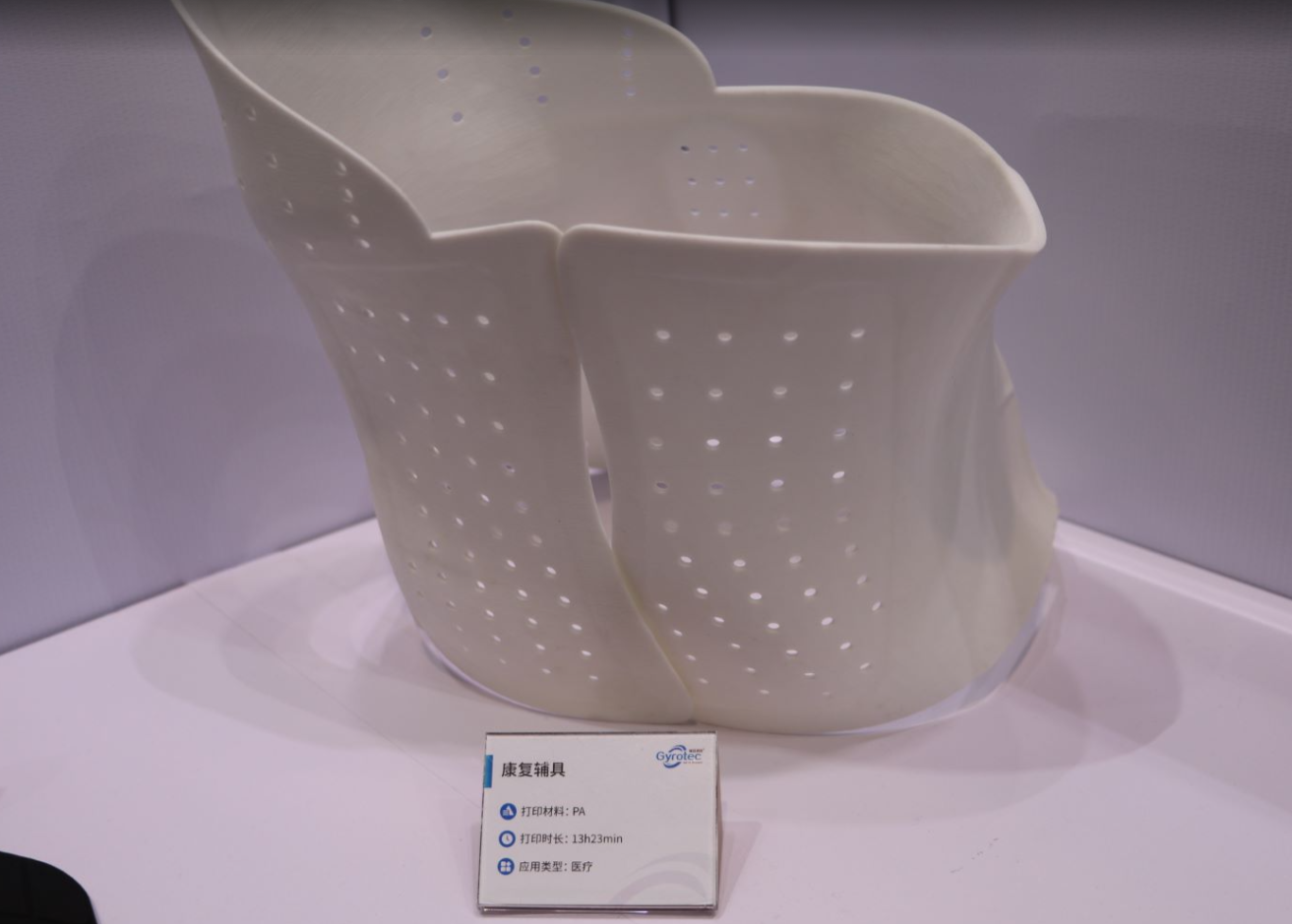
6、医用PA骨生长支架
PA材料也可单独或与聚合物、生物陶瓷材料复合用以制备骨组织工程材料。这主要利用了PA材料与人体细胞的良好兼容性,以及PA材料在人体体液环境中具有的良好化学稳定性。有研究人员利用喷气纺纱技术制备得到了PA6垫片,并模拟人体外体液环境研究了其矿化能力。
也有研究人员利用双注射器静电纺丝技术制备得到了聚氨酯/PA6/明胶复合材料的混合纤维骨生长支架,可诱导磷灰石形成并促进成骨细胞类细胞增殖。PA6纳米纤维材料由于其良好的生物亲和性也被广泛用作骨生长支架材料。
7、药物输送类PA
医用材料PA类药物输送材料早在20世纪70年代便被广泛研究,以期得到一种可控的药物输送系统。药物输送机制主要基于将药物保存在由聚合物形成的微纳米球中,或保存在聚合物基质材料中,并以稳定的速率洗脱药物,实现药物输送。
在PA材料中,主要是通过将PA材料水解,破坏存药微球而实现药物输送。有研究人员通过层层组装技术,得到了创伤修复用含淀粉酶涂层的PA绷带材料。也有研究人员提出了利用PA6的纳米纤维材料或PMMA/PA6的复合材料将药物包覆在聚合物基材中。
利用纳米纤维材料作为药物运送载体的主要优点是其可将药物运送到人体中的特定位置。
此外,不同种类的药物均可以通过直接包覆作用利用纳米纤维材料实现药物输送。药物输送作用也可用于PA缝合线材料中,主要起到缝合伤口组织的微生物灭活作用。
8、创伤修复PA医用材料
PA材料也被用作创伤修复材料修复慢性创伤及烧伤等伤口。
Biobrane®是由PA网、硅胶膜、胶原涂层复合得到的合成生物材料,作为临时的外表皮类似物的皮肤覆盖层,主要在深II度烧伤治疗过程中对坏死组织进行清创术后使用。
TransCyte®与Biobrane®的组成成分类似,被用作切除烧伤后等待自体移植物期间的创伤覆盖物。其由PA网构成,并接种培养了已经失活的来自新生儿包皮的纤维母细胞,其分泌的细胞外基质成分和生长因子有助于创伤生长愈合。
静电纺丝技术也被广泛应用于PA类创伤修复材料的制备中。
三、工业机器人:精密与耐久的“骨骼”与“神经”
机器人对材料性能的要求涵盖轻量化、耐磨性、抗冲击等多个维度。当前,碳纤维、工程塑料、硅材料等均被纳入上游供应链。聚酰胺是五大工程塑料中普及度最高的种类,与其他合成纤维相比,其质地轻盈、机械韧性卓越、耐候性强,且耐磨与滑动特性尤为突出。在机器人制造领域,PA6与PA66尼龙材质备受青睐,它们不仅赋予机器人结构必要的坚固性,还有效缩减了整体质量。
当前,多家材料企业对PA进入机器人市场给予厚望:
预计2025年,PA66的市场规模将达约120亿美元,其中汽车零部件和电子电气领域作为主要应用方向,占据了市场的主导地位。若机器人产业引入尼龙材料,将有望形成“以量促技术”的正向循环。不仅能提升PA6、PA66现有产能利用率,还将加速PA12、PA46等特种尼龙的国产化进程。同时,材料企业与机器人厂商的协同研发,将促进柔性外壳、高载荷关节等专用改性尼龙的开发,助力机器人产品性能和可靠性的提升。
1. 运动系统的核心突破
谐波减速器齿轮:碳纤维增强尼龙(PA12-CF30)替代金属齿轮,摩擦系数低至0.08,无油润滑下耐久性达100万次循环,成为协作机器人关节模组的首选。
行星滚柱丝杠:玻纤增强尼龙(PA66-GF50)螺母部件在120℃高温下运动精度保持0.5μm/300mm,减重60%,应用于工业机器人第七轴驱动系统。
2. 仿生结构的柔性创新
柔性执行器骨架:热塑性弹性体改性尼龙(TPE-PA6)实现300%断裂伸长率与98%形状记忆恢复率,赋予机械手触觉反馈能力,可感知0.1N的微小力变化。
气动肌肉增强层:芳纶纤维/尼龙6复合编织管耐压性能提升3倍,支撑软体机器人连续5万次收缩动作。
3. 感知系统的智能化集成
导电石墨烯改性尼龙薄膜作为应变传感器基材,拉伸15%时仍保持线性响应,集成于机器人手指实现0.5°弯曲角度检测精度。低介电尼龙3D打印天线罩则满足自动驾驶机器人SLAM系统的抗干扰需求。
对于人形机器人这一典型“高交互、高强度、高复杂度”的应用场景,未来对尼龙材料提出更高要求,像耐高温、抗紫外、耐化学腐蚀等,这也将倒逼材料体系进一步向功能集成化与复合化发展。
四、跨界融合:技术迁移与生态重构
尼龙行业的跨界融合正通过技术迁移与生态重构,推动材料科学与产业格局的深度变革。这种变革不仅体现在传统领域的性能升级,更催生了医疗、环保、智能制造等新兴应用场景,重构了从原料到终端的全产业链生态。
1. 产业链协同创新
2. 材料性能的与工艺突破
纳米复合:中科院化学所的MoRh,N/TiO₂催化剂实现尼龙解聚-加氢一步法,将废弃尼龙转化为高附加值化学品,原子利用率达98%。
3. 特种领域的极限挑战
深海机械手:空心玻璃微珠填充尼龙(密度0.98g/cm³)耐压浮力材料在60MPa静水压下压缩率<0.3%,支撑万米级ROV机械手操作。
太空机械臂:NASA开发的尼龙基形状记忆铰链可在-120℃~+150℃温差下自主展开,适应太空极端环境。
核能工业的安全屏障:耐辐射改性尼龙(PA12-HV)在累计吸收剂量100kGy环境下拉伸强度保持率>85%,用于核电站检修机器人防护外壳,保障高危环境作业安全。
4. 产业生态的重构
尼龙材料的 “无限可能”
从汽车轻量化到生物医疗,尼龙材料的跨界突破不仅是技术迭代的产物,更是人类对材料认知深化的缩影。当尼龙66在新能源汽车电池包中抵御高温,当PA11在患者体内承载生命信号,这种诞生于实验室的 “神奇塑料” 正在重新定义材料科学的边界。未来,随着生物基、智能响应、纳米复合等技术的成熟,尼龙将从单一材料升级为 “材料生态”,在碳中和、精准医疗等领域书写新的传奇。正如杜邦创始人华莱士・卡罗瑟斯所言:“材料的终极价值,在于它能让人类的想象力落地生根。” 而尼龙,正是这种价值的最佳注脚。
来源:纤维增强复合材料