碳纤维(CF)是一种碳含量超过90%的无机纤维材料,其分子构造介于石墨和金刚石之间,呈现出混合层状的石墨结构。
CF的主要应用形式是作为承力结构制备CF增强树脂基复合材料(CFRP),具有轻质高强的特点。与普通金属材料相比,CFRP的密度更低,抗腐蚀性能更强。同时,它还具有减震、耐高温和耐疲劳等优点,综合性能优异。
空客A350和波音787的机身上都使用了CFRP材料,且质量占比超过了50%。同时,轻质高强的CFRP在风电叶片、新能源汽车等领域具有巨大的发展潜力,可以有效解决大风力环境下的长叶片材料的密度、强度、模量和耐疲劳性能难以平衡的问题和电池系统下汽车里程低的问题。
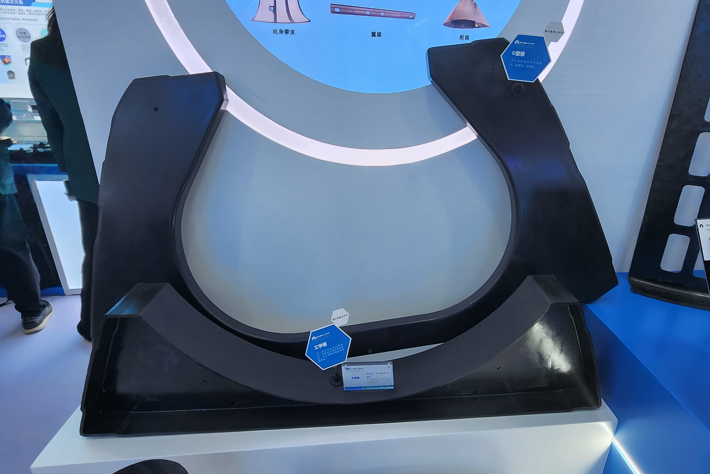
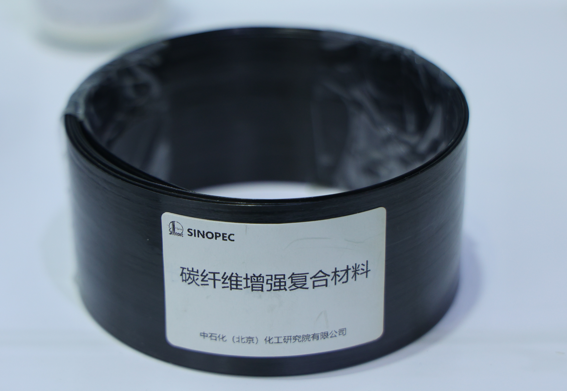
南京聚隆 碳纤维复合材料 工字肋
此外,模拟计算的出现加快了复合材料成型的进程,通过数值模拟纤维增强树脂基复合材料成型过程可以更精确的调控树脂的固化和成型。
目前CF及CFRP成为热点研究方向,是经济结构转型,实现节能减排、绿色发展的优势材料。
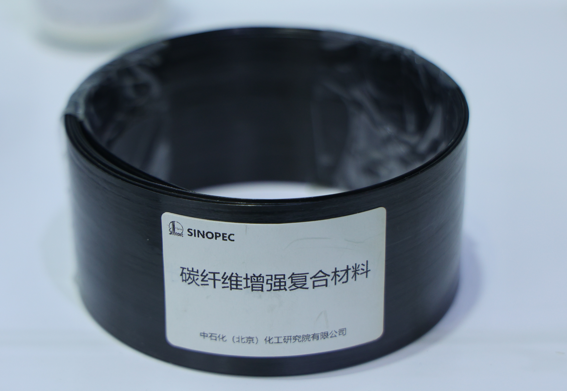
中石化 碳纤维增强复合材料
根据碳源种类,CF可以被划分为黏胶基CF、沥青基CF以及聚丙烯腈(PAN)基CF。其中黏胶基CF防隔热,沥青基CF高导热,PAN基CF不仅兼具良好结构与功能特性,还具有耐高温、耐腐蚀、高比强度和高比模量的特性,是高性能CF的主导品种。
CF的制造工艺涉及聚合、纺丝、预氧化、碳化和高温石墨化等,技术路线复杂,因而CF产品易出现性能差异大、稳定性不足的问题。
日本东丽公司将CF分为四个类型:高强(T700S等)、高强中模(T800S等)、高模(M40等)和高强高模(M50J等)型,国产CF一般也依据上述型号性能分类。
高模碳纤维(HMCF)需要在CF的基础上进行高温石墨化处理,但是石墨化程度的提升也会增加纤维的表面惰性。CF复合材料市场化需要重点解决三方面的问题:CF的表面处理、CF复合材料的低成本成型工艺和终端产业链发展。
界面强度是影响复合材料力学性能的关键,也是研究的重点。因此,本文重点总结了CF表面处理技术和复合材料界面构建方法的研究进展,并从热固性和热塑性树脂两方面阐述了CF与树脂基体适配性的问题,最后展望了CFRP的应用情况和需要持续关注的研究方向。
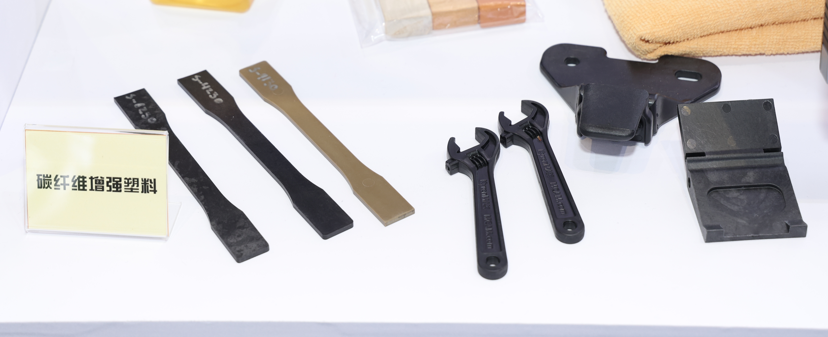
德仪国际贸易 碳纤维增强塑料
一、界面增强理论
界面相是复合材料中的研究重点,界面处理的目的是增强纤维与树脂基体的粘接力,使得复合材料间实现模量的平稳过渡,使纤维和树脂基体间的应力均匀传递,防止应力集中,进而增强纤维复合材料的完整性,提高力学性能。
CF表面惰性、浸润性差,与树脂基体的黏附性差,严重限制了CF基复合材料的发展。纤维和树脂间的结合方式可分为以机械锁合、吸附、范德华力和氢键等为主的物理结合和以共价键等为主的化学结合。界面研究的重点在于纤维和树脂基体间的润湿性、机械锁合和化学结合。
CF复合材料界面增强理论是研究的重点方向,主要包括:
CF由很多石墨微晶组成,微晶尺寸由核到皮逐渐增大,皮层的石墨微晶尺寸大,排列有序,缺陷少,导致CF表面活性碳原子位点更少、表面能更低。因而与树脂的结合性更差。
对CF的表面处理可以增加CF表面活性、粗糙度和润湿度,来提高纤维和树脂的界面黏结,进而提高整体的力学性能。
具体措施为:减少界面缺陷;在纤维表面制造沟壑,以起到机械锁合作用,有益于黏结树脂基体;增强树脂和纤维之间的化学连接。
根据界面增强理论,目前修饰CF表面的方法可分为物理法、化学法及物理化学结合法。主要包括氧化法、化学接枝和涂层等。
图1系统描述了CF、树脂基体两种原材料通过复合材料工艺制备为CFRP,到最终应用的全产业链。
其中,CF难点在于保证高性能的同时降低制备成本,开发不同性能特点和应用场景的CF。树脂的研发难点是保证复合材料最终的性能要求下能够与CF具有较好的浸润性。
热固性和热塑性树脂的改性方法是研发重点。复合材料的难点在于界面相的构建,如何改性CF的惰性表面,提高纤维和树脂间的界面强度是核心问题。此外还需要关注成型工艺,界面相构建需要适配于特定的成型工艺。
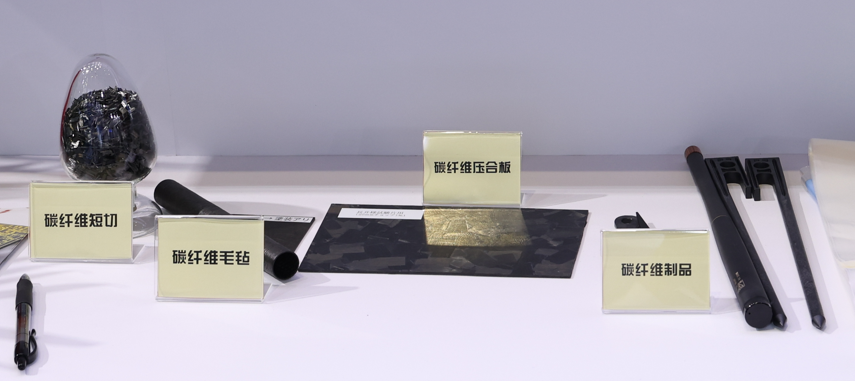
德仪国际贸易 碳纤维制品
1、氧化法
氧化法属于化学结合法,可分为气相、液相和电化学氧化法。气相氧化法一般是采用气相氧化剂使得CF表面生成活性基团的方法。液相氧化法是指在浓硝酸、混合酸或强氧化剂等液相介质中氧化CF。电化学氧化法是以CF作为阳极,碳酸氢钠等作为电解质来活化CF表面。
2、化学接枝法
化学接枝改性属于化学结合,是对CF表面进行接枝处理进而起到活化作用。表面接枝的物质可以分为以下三类:第一类是小分子,如重氮化合物,硝基封端、端氨基重氮分子。
第二类是聚合物,如环氧、超支化聚咪唑等。
第三类是纳米材料,如碳纳米管(CNT)、二氧化硅纳米粒子等。
3、涂层法
涂层法属于物理化学结合法,是在纤维表面涂覆较高粘度和活性的分子或者聚合物。上浆处理、气相沉积和偶联剂处理是较常用的方法。
CF表面处理方法汇总如表1。
氧化法工艺简单,易于操作,能够实现工业化生产,其中气相氧化法的反应条件不易控制,容易损伤纤维的固有强度;
液相氧化法相比气相氧化法反应缓和,但处理时间长,且强酸等危险液体存在风险,会污染环境;阳极氧化法可以在温和的氧化条件下改性CF,且可通过改变电解质获得不同表面活性的改性CF,目前已进入产业化应用,实现了连续化工业生产。
化学接枝法可设计性强,易于操作,效果显著,但是需要检测接枝效果和接枝稳定性,稳定性是其进入产业化应用需要解决的问题。
涂层法使用较普遍,具有设计灵活性高,成本低,实施效果好,适合工业化生产的优点,目前上浆涂层已经实现商业化,但不足处是某些上浆剂的使用会造成环境污染。
此外,应用到纳米粒子改性的接枝法或涂层法需要考虑团聚问题,纳米材料的分散性是实际应用的难题。
三、碳纤维与树脂基体的适配性
纤维与树脂的适配性是复合材料研究的一个关键性问题。树脂的模量、本征黏度、流动性、固化条件和固化后力学性能等是影响纤维和树脂适配性的重要因素。
复合材料不同成型工艺对树脂固化性能等具有不同的要求,树脂的选择也需要根据成型方式的要求确定,不同类型的树脂也需要不同的界面处理方法。
其中热固性树脂表面活性基团较多,而热塑性树脂大多为非极性材料,使其与CF结合难度更高,因而两种树脂的改性侧重点不同。热固性树脂主要侧重于模量改性,热塑性树脂侧重于增加表面活性位点。
此外,由于热固性树脂不能加热熔融,只能一次成型,而热塑性树脂可反复加热熔融,多次使用,热塑性树脂更有利于解决CFRP的回收利用问题。
1、热固性树脂
CF表面惰性,浸润性差,一般CFRP的基体选用环氧树脂。这是由于环氧树脂中含有大量极性羟基、醚键和酯键等基团,粘附力强,与CF结合的难度相对较小。
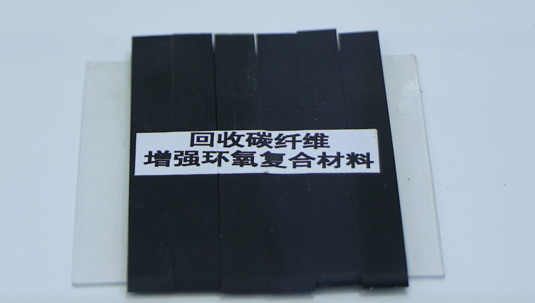
中石化 回收碳纤维增强环氧树脂复合材料
环氧树脂是含有1个以上环氧基团的低分子量预聚物,能固化行成三维网络。按照分子结构可分为缩水甘油类、脂环族、环氧烯烃和杂环环氧。环氧树脂属于热固性树脂,固化后由线型网络转变为交联网络状结构,是不溶不熔的固化物。
其优点是耐热、耐压、不易燃,制品尺寸稳定性好,缺点是脆性较大。CF模量高,增强基体树脂的模量,改善纤维和树脂的模量匹配性,可以在不损伤纤维的前提下提高复合材料整体的界面强度,增强复合材料的刚性。
环氧树脂基体的模量与主链的流动性、分子间作用力和固化交联网络的自由体积有关。树脂基体模量的提高有助于改善HMCF复合材料的界面剪切强度。界面相可以包括CF和上浆剂的界面,上浆剂和树脂基体的界面等。这些不同模量界面层可称为模量中间层,起到平稳连接纤维和树脂的作用。CF模量高于树脂,两者间存在模量差,通过构建模量过渡层可以提高复合材料整体的力学性能。
此外,环氧树脂固化剂也至关重要,一般分为常温固化和加热固化,常温固化剂选用脂肪族多元胺、聚酰胺和脂环族多元胺等,加热固化剂多选用酸酐和多元胺。
2、热塑性树脂
近年来CF增强热塑性树脂的研究也逐渐增多,如聚酰胺(PA)、聚苯硫醚和聚醚醚酮(PEEK)树脂等,具有抗冲击性强、可回收利用等优点。
与此同时,CF增强热塑性树脂基复合材料的研发增多,一方面是高性能热塑性工程塑料研发取得一定成果,具有优良的综合性能,如耐高温PEEK材料;另一方面是可循环CFRP的需求,可反复加工的热塑性树脂有益于可循环回收利用。
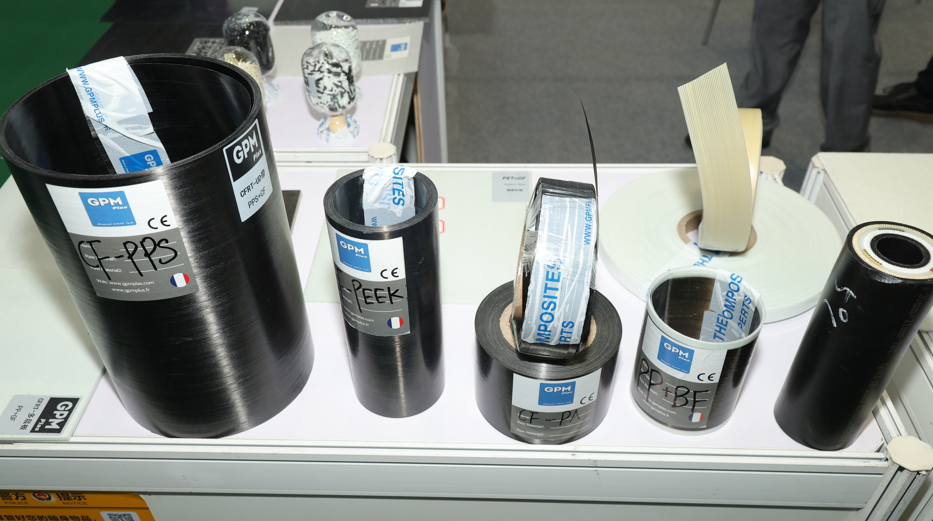
GPM聚普美 CF增强热塑性材料
所以,虽然热塑性树脂与CF界面结合难度高,但其高性能和易回收的优势吸引大量学者对其进行改性研究来适配CF。
热塑性树脂大部分为非极性材料,表面活性基团较少,因而粘附性不如环氧树脂,需要开发适用的热塑性复合材料专用上浆剂。
PEEK是一种热塑性工程塑料,耐高温,熔点为334℃,长期使用温度为240℃,热分解温度为520℃,CF增强PEEK复合材料可耐300℃以上,是优异的耐高温树脂。
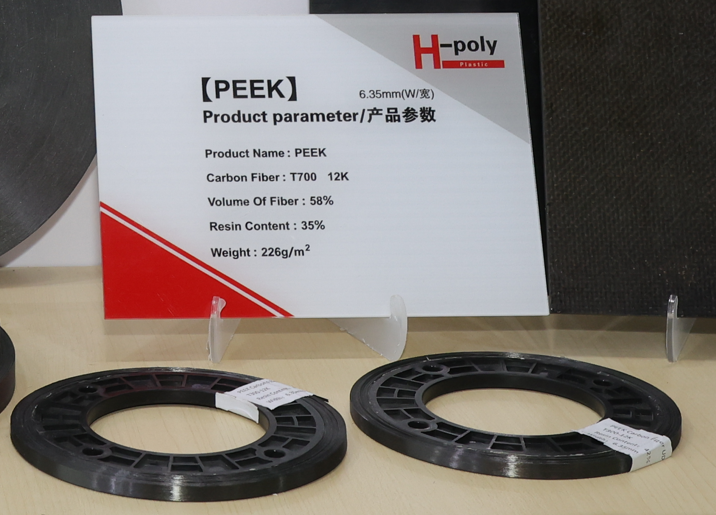
江苏韩塑新材料 PEEK
正是由于PEEK优异的耐热性和化学稳定性导致复合材料界面性能下降。主要存在以下两方面问题:
(1)PEEK常温下不溶,而且熔体粘度高,熔融状态下与纤维的浸润性差;
(2)化学稳定性好,常规加工过程中无法形成化学键等强相互作用。为制备CF/PEEK复合材料必须提高纤维与PEEK基体的适配性,使用有效的改性手段增强界面强度。目前,制备PEEK型上浆剂是增强该复合体系界面强度比较有效的方法。
虽然热塑性树脂与CF的结合相比于热固性树脂更困难,但依靠有效的CF表面改性和树脂改性方法以及开发专用热塑性上浆剂可以推动高性能CF增强热塑性复合材料的开发,是纤维增强树脂基复合材料方面一个重大的进展。
四、应用进展
改性CF和改性树脂基体经过界面结构设计制备为结构功能一体化复合材料,具有轻质、高比强度和高比模量的性能优势,在航空航天、风电叶片以及新能源汽车等领域具有广阔的应用前景等。
1990年,波音公司便采用碳纤维预浸料用于波音777的主机身结构。目前,CFRP在波音787上已应用到机身、主翼、尾翼和襟翼,而波音767主要用于襟翼,CFRP质量比从3%提高到了50%,波音787的质量显著减轻,并节省了20%-22%的燃油。
空客A350也主要使用了CFRP,质量达到53%。私人飞机和直升机的CFRP的使用量已达到70%-80%。
CFRP在飞机上的应用从副翼、翼片和方向舵等开始,随着复合材料力学性能的研发进步,能够应用于机身、垂直尾翼和机翼等主要结构,并逐渐取代轻质金属合金。
CFRP除作为结构材料外,其导电性能也被设计用于防雷涂层。
CFRP的应用需要关注树脂基体的改性研究。低成本大丝束CF复合材料的超薄化是促进CFRP产业化的一个趋势,超薄预浸料具有厚度薄、设计好、屈曲角小等优点,能够延迟基体开裂和分层。但是,常用的环氧树脂并不能满足这一要求。
随着风电产业的发展,为降本增效,风电叶片逐渐大型化。大型风电叶片可以增大年发电量,同时可以减少风电机组占用土地面积和安装等成本,有利于降低度电成本。
目前风机叶片长度向160m发展。大型化的风机叶片对材料的强度、模量、密度和耐疲劳性等性能提出了更高的要求,无碱玻纤/织物的模量约为40GPa以上,而纯CF织物、预浸料和拉挤板的模量提高到了120GPa以上,传统玻璃纤维的强度和模量已经不能满足需求,轻质高强的CF展现出比玻纤更大的优势和必要性。
国外风电叶片基本都转向CF技术路线,50~120m叶片大部分都采用CF,国内CF主要应用于海上百米级风电叶片。风电叶片材料的优化进程主要是材料质量、性能和成本的优化过程。
随着CF原丝和碳丝成本的降低,CF在风电叶片领域的应用占比会大量提升。风电叶片的增强材料主要用于主梁和叶片根部,一般选用连续纤维作为增强材料,热固性树脂来黏结和支撑增强材料,其中热固性树脂主要选用环氧树脂。
CF叶片主要应用类型为拉挤板。因为拉挤碳板相较于预浸料和织物而言,缺陷少,纤维含量更高,从而性能更高,且能够连续成型,易于自动化,质量稳定,适合大批量生产。
拉挤工艺用树脂基体的要求为粘度低、适用期长和固化收缩小,长叶片用环氧树脂还要求具有优良的弯曲强度和结构性能。拉挤工艺用的CF使用前必须经过表面处理,增大树脂的浸渍性,未来研发的方向是开发专用的风电拉挤用CF及适配的改性树脂。
新能源汽车的质量问题是影响汽车续航里程的关键问题。汽车质量每降低10%,续航里程约提高5.5%。将轻质高强的CF复合材料作为新能源汽车承重件,不仅可以大幅降低汽车的质量,也增强了汽车的强度、减震特性和耐疲劳使用性能,达到了降低能耗和增加续航的目的。
目前CFRP已经应用于车门、引擎盖和行李箱盖等车身覆盖件;车身、顶盖、座椅和底盘等车身结构件;轮毂、制动盘和内外饰材料等。
CFRP用于新能源汽车的车身,将其代替钢铁等金属材料,质量可以降低40%~60%。英国的减重实验表明CFRP制作的车身质量172kg,相比钢制车身的368kg,减重约50%。
车用CF复合材料主要应用大丝束CF,成型工艺有湿法模压和快速成型工艺等,具体包括预浸料压缩成型、模压成型、高压树脂传递模塑和注塑成型等。
目前常用的是CF增强环氧树脂复合材料,成型过程中大丝束CF与树脂的结合性提升是关键,可以选用机械打磨和上浆处理CF,改性环氧树脂使其适配成型工艺等组合改性方法提高界面结合强度。
参考资料:碳纤维增强树脂基复合材料界面改性及应用进展,刘柳薪,卢晓英,吴颖,荔栓红,吴谨妤,袁文静,高源
原文始发于微信公众号(艾邦高分子):碳纤维增强复合材料(CFRP)界面改性及应用进展