使用轻质材料来降低汽车质量已成为实现新能源汽车轻量化的重要途径之一。
随着材料领域的不断发展,玻璃纤维增强复合材料、碳纤维增强复合材料等多种轻量化的纤维复合材料开始应用在新能源汽车领域。
低密度、高强度、耐腐蚀、耐疲劳的碳纤维复合材料是汽车领域应用最为广泛的高性能纤维复合材料,在汽车众多系统部位都有着大量应用,比如:车体的车门、车顶等;发动机系统中的推杆、摇杆、水泵叶轮;传动系统中的传动轴、离合器叶片;底盘系统中的车底框架、悬置件、弹簧片等。
随着新能源汽车的快速发展,其电池的安全储存问题一直是研究关注的热点,电动汽车电池包壳体是目前新能源汽车能量储存的主流方式,优点众多的碳纤维复合材料在此领域也开始崭露头角。
碳纤维一般不会直接使用,通常作为增强体,与树脂基体、金属基体、陶瓷基体等结合形成碳纤维复合材料。图1为碳纤维布及碳纤维复合材料型材实物图。
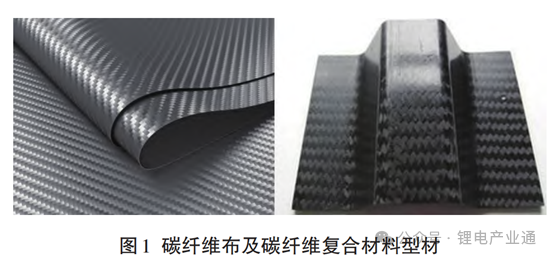
①低密度、高强度,密度仅为1.5~2.0g/cm3,相当于轻质铝合金密度的1/2,强度是钢的4~5倍、铝的6~7倍;
②耐高温、耐低温,碳纤维的热弹性系数小,在3000℃非氧化气氛下不融化、不软化,在液氨温度下依然不脆化;
③良好的导电性,25℃时,高模量碳纤维的比电阻为775Ω·cm,高强度碳纤维的比电阻为1500Ω·cm;
按照原丝种类、力学性能、丝束大小可以将碳纤维分成以下几类,具体见表1。
|
|
|
|
|
成品品质优异,工艺较简单,产品力学性能优良,已成为碳纤维主流
|
|
原料来源丰富,碳化收率高;原料调制复杂,产品性能较差;目前规模小
|
|
高耐温性;碳化收率低,技术难度大,设备复杂,成本高;主要用于耐烧蚀材料及隔热材料
|
|
|
以1K、3K、6K为主,逐渐发展为12K和24K,是宇航级碳纤维
|
|
48K及以上碳纤维,包括60K、120K、360K和480K等,是工业级碳纤维
|
|
|
|
|
|
碳纤维通常作为增强材料使用,因此实际使用中通常按照力学性能进行分类,主要依照拉伸强度和模量进行分类,高强型的强度为2000MPa、模量为250GPa,高模型的模量在300GPa以上,超高强型的强度大于4000MPa,超高模型的模量大于450GPa。
根据欧洲铝协数据,当汽车质量降低10%时,能源使用效率将提高6%~8%,百公里排放污染物降低10%。而对于新能源汽车,100kg的质量减小相应可以增加其续航能力约6%~11%。
轻质高强的碳纤维复合材料在汽车上有着丰富的应用,表2为部分车型应用碳纤维复合材料的情况。
生产商
|
车型
|
应用部位
|
效果
|
宝马
|
i3i8
|
车身life模块
|
质量减小250~350kg
|
奥迪
|
RS5COPE
|
车顶
|
质量减小40%
|
奔驰
|
E级轿跑
Superlight
|
车身
|
质量减小350kg
|
丰田
|
丰田86
|
传动轴
|
质量减小50%
|
上汽
|
荣威E50
|
引擎盖
|
质量减小37.5%
|
华冠
|
前途K50
|
车壳
|
相比传统钢材质量减小40%以上
|
富士
重工
|
野马GT350R
|
轮毂
|
较原铝合金制件质量减小43%
|
斯巴鲁WRS
|
车顶
|
较原钢板质量减小80%
|
图2为中泰证券研究所2020年对全球汽车碳纤维市场规模及预测统计,预计到2025年全球车用碳纤维市场规模可达2.01万t。
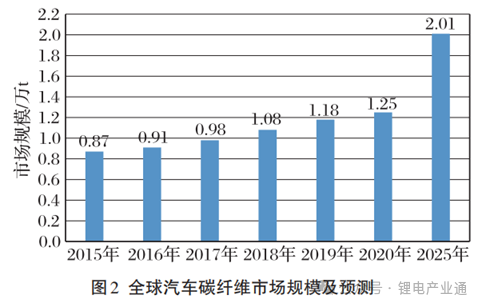
动力电池包是新能源汽车的动力源,由壳体包覆电池模块而构成电池包主体。电池包壳体对电池模块的安全工作和防护起着关键作用,要求其材料具有防腐蚀、绝缘、耐常温和低温(-25℃)冲击以及阻燃等特性。图5为新能源车动力电池包及电池包分解图。
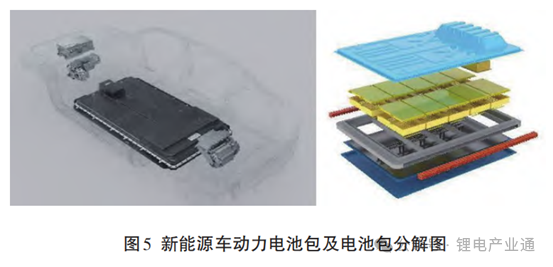
作为电池模块的承载体,电池包壳体对电池模块的稳定工作和安全防护起着关键作用,一般是安装在车体下部,主要用于保护锂电池在受到外界碰撞、挤压时不被损坏。
传统车用电池箱体采用钢板、铝合金等材料铸造,然后对其表面进行喷涂处理。随着汽车节能环保和轻量化发展,电池壳体材料也出现了玻璃纤维增强复合材料、片状模塑料、碳纤增强复合材料等多种轻量化的材料选择。
钢制电池包壳体是最原始的动力电池包壳体材料,一般采用铸造钢板焊接而成,具备强度高、刚性高的优点,但其密度大、质量大,需要增加防腐蚀工艺。
铝合金壳体是目前主流的动力电池包壳体材料,具有轻质(密度仅为钢的35%)、易加工成型、耐腐蚀等特点。
随着汽车的轻量化发展,以及热固性塑料成型技术的开发,新型塑料及复合材料开始逐渐被用作电池包壳体材料。热固性塑料电池包壳体自身质量为35kg,比金属箱体的质量约小35%,可承载质量为340kg的电池。
具备众多优点的碳纤维复合材料已成为传统金属材质电池箱体的理想替代品,在部分车型上已有了初步应用。
蔚来与德国SGL Carbon联合开发了84kW·h碳纤维电池包,该碳纤维壳体质量比铝结构减小40%,能量密度大于180(W·h)/kg。
蔚来展示的84 kW · h碳纤维电池包壳体
天津中科先进技术研究院与力神合作开发的碳纤维复合材料电池包壳体的总质量约为24kg,较铝合金结构质量减小50%,能量密度高达210(W·h)/kg。
段端详等对碳纤维复合材料电池包壳体进行了轻量化设计和铺层工艺优化,在满足相关工况条件下,得到的壳体质量较钢结构减小了66%。
赵晓昱等采用碳纤维复合材料,利用刚度等效设计法对电池包壳体进行轻量化设计,相比于钢结构质量减小64%~67.6%。
LIU等采用RBDO方法解决碳纤维复合材料电池包壳体上盖轻量化设计问题,在性能满足要求的情况下,实现质量减小22.14%。
谭礼忠等对1.5mm厚度铝上盖(方案一)、1.5mm厚碳纤维上盖(方案二)和0.5mm碳纤维+3mm厚蜂板+0.5mm厚碳纤维复合上盖(方案三)三种方案进行对比研究,发现方案三为最优,相对于方案一可减小质量31%。
芳纶混杂碳纤维制成的电池包壳体在国内外也有了相关研究,以南京奥创先进材料科技有限公司为代表的高性能纤维公司也开始了相关研究,并在专利领域开始布局,如专利CN113764801A等。
受限于成本问题 , 目前以碳纤维复合材料为主的高性能纤维复合材料在电池包壳体领域并未得到大面积应用 ,相信随着新能源 的发展以及纤维复合材料应用的扩大 ,纤维复合材料的使用成本将逐步降低 ,未来新能源市场上纤维复合材料也会大放光彩。
参考资料:碳纤维复材在氢气储存和电池包壳体的应用现状,李宗家等
原文始发于微信公众号(艾邦高分子):碳纤维复材在电池包壳体的应用现状